
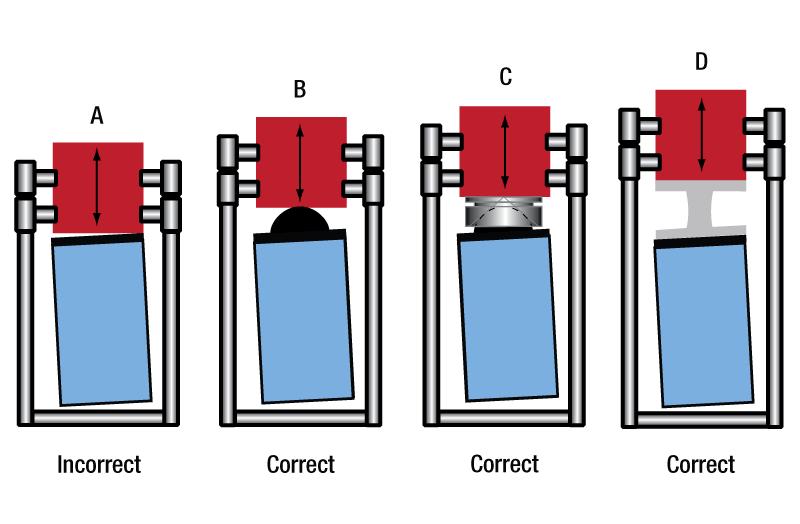
An ideal device for wearable tactile interfaces should be light weight, compliant, safe, and incorporate multiple sensing and actuation points over a distributed surface. Linear resonant actuators have improved efficiency and a compact size compared to electromagnetic eccentric motors ( Mortimer et al., 2007) but still suffer from problems of rigidity, complexity, and narrow bandwidth. These solutions have certain limitations for wearable applications due to bulkiness, rigidity, and complexity. The majority of vibrotactile systems developed so far have used electromagnetic eccentric motors ( Shahoian et al., 2004), electrostatic piezo actuators, or electro-active polymer-based actuators ( Koo et al., 2008). Therefore, for effective tactile sensing, the operational frequency range is selected between one of the two along with a minimum spatial resolution of 1–2 mm for human fingers ( Kaczmarek et al., 1991 Asamura et al., 2001). The mechanoreceptors responsible for vibrotactile sensation are the rapidly adapting (RA) and Pacinian corpuscle (PC) receptors with perceptible frequencies ranging from 3 to 100 and 100 to 400 Hz, respectively ( Choi and Kuchenbecker, 2013). In general, tactile sensation is perceived through four different types of mechanoreceptors inside human skin. The human tactile sensory response is limited in frequency range, and both temporal and spatial resolution making the determination of the vibrotactile actuator’s specifications difficult. In wearable devices, vibrotactile feedback is considered as one of the safest and most popular ways to interact with the human body ( Lindeman et al., 2006 Choi and Kuchenbecker, 2013). The devices required for providing kinesthetic feedback are comparatively large and heavy ( Hirose et al., 2001 Shahoian et al., 2004 Viau et al., 2004 Takahashi et al., 2008) and thus less suitable for a wearable scenario. Haptic feedback is generally divided into two classes – namely tactile and kinesthetic. The use of haptic feedback has proven effective in aided rehabilitation in subjects following stroke or paralysis ( Viau et al., 2004 Takahashi et al., 2008 Alahakone and Senanayake, 2009 Kapur et al., 2009 Wall, 2010 Carmeli et al., 2011). Over the past decade, research on the use of robotic haptic devices in neuro rehabilitation has accelerated ( Maciejasz et al., 2014). Experimental findings show that this ultra-thin SPA and the unique integration process of the discrete lead zirconate titanate (PZT)-based piezoelectric sensors achieve high resolution of soft contact sensing as well as accurate control on vibrotactile feedback by closing the control loop. We examine in detail the mechanical performance compared to the SPA model and the sensitivity of the sensors for the application in vibrotactile feedback.
#PIEZO ACTUATOR AND SENSOR SKIN#
We describe the design and fabrication of a 1.4 mm-thick vibratory SPA – skin that is integrated with piezoelectric sensors. This paper describes a soft pneumatic actuator (SPA)-based skin prototype that allows bidirectional tactile information transfer to facilitate simpler and responsive wearable interface. Although there have been various research efforts in creating tactile feedback to improve various haptic interfaces and master–slave manipulators, we are yet to see a comprehensive device that can both supply vibratory actuation and tactile sensing. Evidently, such interfaces require flexibility and conformity without losing their functionality even on rigid surfaces. The latest wearable technologies demand more intuitive and sophisticated interfaces for communication, sensing, and feedback closer to the body. Reconfigurable Robotics Laboratory, Institute of Mechanical Engineering, Ecole Polytechnique Fédérale de Lausanne, Lausanne, Switzerland.
